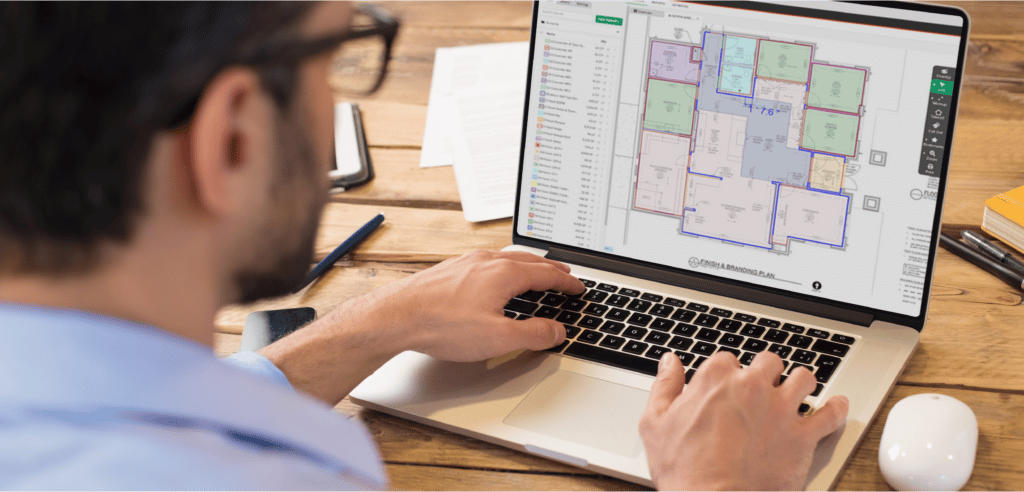
If you’ve previously worked in residential construction and are moving into commercial projects, you might be unfamiliar with construction takeoffs and how they work. Once you have a basic understanding of how takeoffs fit into the commercial construction process and why they’re necessary, along with steps for choosing the right takeoff tool for you, you’ll quickly get the hang of it and will be performing accurate takeoffs in no time.
What Is a Construction Takeoff?
In a nutshell, a construction takeoff is counting or measuring items on blueprints to determine how much material is needed to complete a job.
Many residential contractors are experts at eyeballing a house to estimate the amount of materials that will be needed for a job. This is an admirable skill, but it’s one that doesn’t translate well to high volumes of commercial projects.
Generating extremely accurate construction estimates for commercial work is crucial for success. You need to know the precise amount of materials on structures that are often very large and complex, and you’ll be bidding on multiple jobs at once. A ballpark guesstimate might leave you leeway with materials you could reuse later, but you’ll have to pay for them upfront, which could cramp your cash flow. And, adding a significant markup to cover your costs could price you out of the job. Many general contractors do takeoffs to check your work, and some will even want to see your completed takeoffs. There’s no getting around the process.
In large, well-established commercial contracting companies, often a team of estimators shares responsibility for takeoffs. The chief estimator may be in charge of handling the company’s bid calendar and assigning projects to the rest of the department, and often senior estimators will follow behind less experienced members of the team to check their work and provide feedback.
In smaller companies, until it’s feasible to hire more staff, the owner or a single estimator will handle all takeoffs, but this practice is unsustainable for the long term if the business aims for substantial growth.
It’s not only construction estimators who perform takeoffs, though: in some organizations, people whose primary function is sales also perform takeoffs, as do some material suppliers.
Quantity Takeoff vs Material Takeoff
The two types of takeoffs are quantity and material takeoffs. The main difference in the two is that quantity involves counts while material involves measurements.
Quantity takeoffs are required when you simply need to get counts of a type of material needed. Contractors in MEP trades are frequent users of quantity takeoffs, but most trades do quantity takeoffs to some degree. They’re typically used for determining material counts for items like:
– Electrical outlets
– Light fixtures
– Bathroom fixtures
– Doors
– Windows
– Signage
– Sprinkler heads
Then there are material takeoffs, which involve performing measurements and applying formulas to determine how much material is needed. Most trades also perform material takeoffs Tools like masonry takeoff software are invaluable for accurately measuring materials for tasks like laying bricks or constructing stone walls. Some examples include measuring:
– Linear feet for installing and painting baseboards, trim, or parking lot lines, or running cable and wire
– Surface area (square feet) for installing drywall, flooring, or sloped roofing, or for painting walls
– Volume (cubic feet or yards) for civil and site work such as pouring concrete slabs or walls, or laying asphalt
Note that while quantity takeoffs result in the exact amount of materials needed for a job, material takeoffs require assigning items and assemblies to your measurements so you can calculate quantities based on how materials are packaged and sold. For example, if you need to pour a 6-inch slab of concrete, and you measure out 400 square feet, you’ll need to buy 445 60-lb bags of concrete, or 334 80-lb bags.
6 Steps: How to Do a Full Construction Takeoff
Now that we’re clear on what a takeoff is and why it’s an important part of preconstruction, let’s dive into the actual steps to complete a takeoff.
Step 1: Access the Project Plans
Before you can start a construction takeoff, you have to review the project plans. This might be done via email if you’re on a general contractor’s bid list, or you might download plans from a planroom. The project plans will provide the information you need to make a materials list.
Step 2: Identify Relevant Pages
Often you’ll receive every blueprint page of a project, when you only need the ones that are relevant to your trade. In a manual takeoff, this might mean a significant amount of time spent paging through and examining specs. With a digital takeoff tool, you can simply conduct a plan search for keywords.
Step 3: Determine Your Material Needs
Once you’ve narrowed down the relevant pages, you can begin reviewing the blueprint. Start listing out the types of materials and quantities that the plan requires.
If you’re doing a manual takeoff, you’ll have to count each item yourself. Or, with the help of digital takeoff tools you can automate the counting process. With auto count software, all you have to do is review the list and make a few modifications if needed.
Step 4: Verify the Scale
For a material takeoff, you’ll need to set or verify the scale on the plans. With paper plans you can use a ruler. With digital plans, use point and click on your software to measure the longest known distance and determine what an inch represents on your plans. For example, flooring industry software can easily calculate dimensions and areas for accurate material estimates, streamlining the entire project process. Some takeoff tools also provide common scales for you to choose from.
Step 5: Calculate Material Quantities
Once you verify the scale you can confirm important measurements like square footage that impact the quantity of materials you need for the project. Depending on your tools, this could be as simple as pointing and clicking with your mouse or as complex as maneuvering your scale ruler over printed plans and marking down distances on a sheet of paper.
Measure like items first, and each time you switch to a different type of measurement, update your items and assemblies accordingly.
Step 6: Add Up the Costs
Once you have a list of materials and you know the size and amount you need of each, you can begin calculating your final costs. Good materials takeoff software will perform this step automatically. For manual takeoffs, you’ll likely need a calculator to perform this step.
Determine the price of each material and then add those together to come up with the final estimate.
Bid Faster. Win More. Build Smarter.
Get your FREE account today to:
- Increase Team Efficiency
- Complete Estimates Faster
- Generate More Revenue
What Happens after the Construction Takeoff?
When your measurements are finalized, it’s time to create a cost estimate. This is where, as an estimator, you get a chance to use your skills — especially when supported by a reliable construction estimating software that helps you calculate total project cost with confidence.
You’ll have a clear picture of the material costs from your takeoff, and you’ll ideally have a good indication of the profit margin you need to make for the job to be worthwhile. You’ll take these two numbers and factor in other direct costs, indirect costs, and markup to get your final selling price.
First, add in overhead costs that you’ve determined and broken out to be distributed across your projects. These are the expenses it takes to keep your business afloat, like rent for office space, utilities, insurance, office staff salaries, software subscriptions, trade association dues, etc.
Then you’ll want to take into consideration any non-material costs associated with the job like equipment rental or waste disposal. At this time, also factor in your labor hours: how much material can one person on your crew install in a given hour? How many people do you need onsite to get the job done, and for how long? Don’t forget to also account for sales tax so you can pass that cost on to the client.
Now you have your full project cost and you can use your discretion at how much to mark up your price from this number to reach your desired profit, or as close as you can reasonably get to it. But you’ll know for sure you can’t go any lower than your project cost or you won’t break even on the job.
At this point, you can generate a proposal from your final estimate and provide it to the general contractor in the format they prefer, whether that is email or through the planroom, and wait to hear if you’ve won the bid.
What Makes a Successful Construction Takeoff?
A successful takeoff begins with a correctly set scale. Usually the architect will include a scale on the blueprints, but not always, and there are cases in which the scale provided is inaccurate. So the takeoff process should always begin with checking or setting the scale; otherwise all of your measurements will be off.
The key to mastering successful takeoffs is being thorough and accurate, while also keeping speed top of mind. The best takeoff and estimate won’t win any bids if it’s not submitted on time. Ensure that your team knows how to find everything they need on plans, that they understand how to apply items and assemblies to get accurate quantities from their measurements, and that they have the skills they need so they’re set up for success.
Common Construction Takeoff Pitfalls
The most common mistakes that happen in the takeoff process come down to missing deadlines and inaccurate measurements.
With manual takeoffs in particular, it’s not uncommon for an estimator to work late into the night trying to complete a takeoff only to miss a bid deadline because the extended time it took to do the takeoff left no room for the critical step of creating that detailed estimate. Trying to do a thorough, thoughtful estimate in a time crunch is not conducive to success, and often this leads to wasted hours spent on the takeoff only to not even get a shot at the job. Using reliable quantity takeoff software can drastically reduce manual errors and improve efficiency across all project phases.
Inaccuracies can happen with manual takeoffs or with a cumbersome digital process that involves multiple software tools cobbled together. In both cases, you’re moving data from one tool to another – paper to Excel, or takeoff software to estimating software or Excel – and opening yourself up to mistakes. Manual data entry needs only a single distraction or typo for an estimator to lose track of their place or throw an estimate off significantly.
The best way to avoid these pitfalls is to adopt takeoff software to help you streamline your inefficient workflow.
The Real Purpose of a Takeoff in Construction
The takeoff itself is just one part of the preconstruction process, leading up to creating an estimate and proposal. Your objective with performing takeoffs is to create a clear picture of the cost of materials needed to do a particular job. When you’ve determined that number, you can then begin to account for non-material costs, like labor hours, overhead, sales tax, and any other indirect costs.
The construction estimate is where you apply all of these costs together to generate a total project cost: this is how much you’ll have to pay out of pocket to complete the job at hand. From here, you’ll be able to make the jump to how much you should mark up your selling price to reach your desired profit margin.
So, because the construction takeoff, though very important, is not the only task to complete before a bid, setting a goal for speeding up your takeoff process could be the best way to put your company on a path to growth. A cumbersome, time-consuming takeoff workflow means less time for your team to put their analytical skills to use crafting estimates that will win you bids and earn you profits.
How to Speed Up Your Workflow: The Benefits of a Digital Takeoff Process
Historically, takeoffs were done on actual printed blueprints, and some contractors continue to use this outdated manual takeoff method. Some of the problems associated with manual takeoffs include:
– Printing blueprints is cost prohibitive, and significant amounts of time can be eaten up by scheduling at specialty print shops and picking up plans.
– Storing printed blueprints takes up valuable office space and puts you at risk of losing or damaging expensive plans in the time between printing and the start of a job.
– Conducting measurements on paper is time-consuming and prone to human error. The time crunch of a manual takeoff means that bid deadlines can get missed and also that an estimator doesn’t have the brain space necessary to produce their best work.
Converting to a digital takeoff process eliminates these drawbacks. On-screen takeoffs offer substantial benefits such as:
– Up to 10 times faster takeoffs
– Digital storage for easy access to plans and documents
– Simplified collaboration among colleagues
– Ability to work from more than one device or location
– Reduced rework and manual data entry
– Higher levels of accuracy in measurements
– Easy access to historical data for project review and forecasting
With the right software tools, digital takeoffs set your team up for more success during estimating by allowing you to seamlessly create a bill of materials for suppliers and incorporate labor and materials using pre-built and customizable libraries. But that’s not all: they also provide insights into your team’s performance and schedules. A digital takeoff tool that offers a bid calendar allows you to understand which bids each team member is working on at a given time, what their workload looks like, and what their win rate is. You can see where someone is succeeding or where they are struggling and might need help. You can also export data from your digital takeoff platform to determine the types of jobs that bring in the most profit so you can make better long-term decisions about which projects to seek out and bid on.
Software Packages for Construction Takeoff and Estimating
If you’ve been doing manual takeoffs, it can be tough to bite the bullet and decide to purchase software, but you’ll see that in most cases, it’s the best decision for your business. The only exception is if you do very few takeoffs: for example, if you primarily work in residential construction and only do one or two commercial projects each year. In this case, a software subscription might not be best for you, but consider looking for options that offer a free version that you can still take advantage of for your few takeoffs, and that you’ll then be familiar with if you do expand into more commercial construction cost estimating farther down the road.
Advanced Digital Takeoff Techniques
Construction technology is constantly changing, and it’s important to stay up-to-date with the latest developments. Two game-changing features that are newer to the field are artificial intelligence and aerial image takeoff.
Increasing Efficiency with Artificial Intelligence
Artificial intelligence gets a lot of attention, both positive and negative, but the fact is, it’s here to stay, and it can really transform your takeoff process. Think of AI as your assistant, not your replacement. You can use AI to automate time-consuming processes to free up your team for crucial tasks. Automate counts for doors, windows, and symbols; takeoffs for interior and exterior walls; and takeoffs for gross areas and room areas.
The benefits of incorporating AI into your preconstruction process are manifold and include:
– Reduced manual errors: AI systems reduce the likelihood of human error by automating repetitive and detail-oriented tasks. This ensures higher accuracy in material counts and measurements, reducing costly mistakes during construction.
– Faster workflow and turnaround: AI can process large amounts of data quickly, completing takeoffs in a fraction of the time it would take manually. This allows project teams to focus on other critical tasks, such as creating detailed estimates or communicating with clients.
– Cost savings and efficiency: By reducing the time spent on takeoffs and minimizing errors, AI helps lower the overall cost of the project. Accurate takeoffs also prevent over-purchasing or underestimating materials, leading to more efficient resource management.
– Scalability and adaptability: AI tools can easily scale to handle larger projects or more complex designs. Whether working on a small residential build or a large commercial development, AI can adapt to the project’s needs.
Utilizing Aerial Imagery for More Accurate Takeoffs
For exterior projects that do not have blueprints, using aerial image takeoffs is beneficial for contractors because they provide high-quality, up-to-date images that improve measurement accuracy and speed up estimating processes. Unlike traditional methods that require climbing buildings or using low-resolution satellite images, aerial images offer multiple views (top-down and oblique) that enhance understanding of surfaces and angles. This approach reduces risks, saves time, and allows for seamless integration with takeoff and estimating tools, leading to more polished proposals and efficient project planning.
What Are Cloud Takeoffs, and Why You Should Use Them?
A cloud takeoff is simply a construction takeoff performed on software that is cloud-based rather than desktop-based. To understand what this means, remember that before the cloud became common, typical software tools were available on a license basis for individual devices – typically desktop computers. Companies had to buy a license for each computer that the software would be installed on, and it could only be accessed via that particular device. A user would log on to their computer to do a takeoff and then, if any colleagues needed to be involved, they’d have to download the plans and email them to their coworker, who would then download to their desktop and upload into their own copy of the software.
Not only is this a time-consuming process, but it also opens up more room for – you guessed it – user error. With no way of knowing for sure which version of a file was the most up-to-date, rework would often occur, and if one person was out of the office unexpectedly, work would grind to a halt with no way to access their progress or see what they’d been working on.
Many old-fashioned desktop construction takeoff software options still operate in this outdated way, believe it or not. So be sure when you’re evaluating tools to choose one that offers cloud takeoffs.
In addition to speed, advantages of cloud takeoffs include:
– Version control for digital blueprints
– Real-time collaboration among colleagues
– Access from any device, any time
– Cloud storage for simplified organization
– Free and instant software updates
– Better security and disaster recovery
– Reduced rework
– More scalability and flexibility
Cloud takeoff software will make your takeoff process faster, smoother, and more accurate. It will transform the way your company does preconstruction and can be the catalyst for enormous growth and increased profits.
But remember that the best takeoff tool is still only a tool, and you need skilled estimators to wield it.
As Andy Boyd, Vice President at Galindo & Boyd Wall Systems LLC in Texas, says in an AWCI article on the past, present, and future of estimating, “[A]t the end of the day, estimating still requires an experienced individual to sit down and peel the project apart, piece by piece, detail by detail and page by page to get a handle on what all will be required to build the project.”
So choose a cloud takeoff tool that will get you great results, and staff your estimating department with strong analytical thinkers and experienced estimators who can use the software in tandem with their own skills to take your business to new heights. When you are looking for solutions for takeoffs or the right construction cost estimating software, we are here to help.
If you’re in the market for takeoff and estimating software, we invite you to create a FREE account with STACK and take it for a spin.